Start of the DFG project to develop predictive models for deviated thermo-elastohydrodynamically lubricated contacts (DeviaTEHD) in February 2023
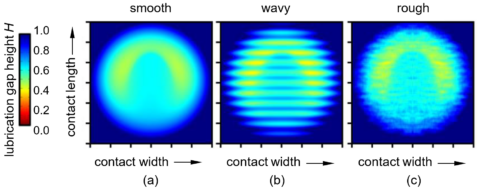
In the context of resource minimization and the development of energy-efficient and wear-resistant technical products, the reduction of friction losses in lubricated contacts of machine elements is of great importance. These losses mainly depend on the lubrication condition, the component geometry as well as the type of motion of the system. However, significant friction losses can also be attributed to manufacturing-related deviations of the surface topography. A computational consideration of the shape deviation of the surface of lubricated thermo-elastohydrodynamic (TEHD) contacts has only been carried out within the framework of time-consuming and complex simulations so far. Previously established, less complex calculation methods, such as analytical approximation equations developed by DOWSON/HIGGINSON and BLOK/MOES for calculating the lubricant film heights and associated further correction factors, do not yet comprehensively take surface deviations into account.
The aim of this project of the German Research Foundation (DFG) is to close this research gap by developing prediction models for lubricated TEHD contacts involving infinite line contacts and three-dimensional point contacts in order to enable a rapid calculation of the lubricant film heights, the pressure and the temperature, taking into account the shape deviations of the surface. Hence, a contribution shall be made to design and calculate TEHD contacts, as they are found for example in gears or roller bearings, in a more energy-efficient and wear-resistant way. To generate the necessary database, the already existing and established TriboFEM KTmfk simulation tool is used, which takes into account the macro and micro geometry of the component. The validation of the prediction models is carried out, among other things, by means of experimental investigations on the pin/disk-tribometer. Finally, the project includes the application of the developed prediction models for the friction calculation of cylindrical roller bearings.